As industries increasingly focus on sustainable solutions, additive manufacturing (AM) remains at the forefront of innovation due to its ability to reduce material waste and production costs. Stratasys, a leader in AM technology, has taken a significant step forward with the introduction of SAF ReLife, a pioneering software solution that repurposes waste PA12 powder, traditionally seen as a costly byproduct. Released on November 6, 2024, SAF ReLife enables manufacturers to transform leftover powder from various AM processes into high-quality parts using Stratasys’ H350 printer.
With SAF ReLife, Stratasys is addressing not only the economic and logistical challenges of leftover powder but also the broader environmental concerns tied to waste in AM. This article delves into the SAF ReLife technology, its practical benefits, real-world applications, and how it serves as a potential solution to current sustainability challenges within AM.
What is SAF ReLife?
SAF ReLife is a software-driven solution designed to recycle and repurpose waste powder generated from powder bed fusion (PBF) technologies, such as selective laser sintering (SLS), jetting, and high-speed sintering. By feeding this recycled powder into the Stratasys H350 printer, SAF ReLife allows manufacturers to create functional, high-quality parts from what was previously considered waste. This technology is the latest innovation based on Stratasys’ Selective Absorption Fusion (SAF) technology, aimed at maximizing resource efficiency.
Key Benefits of SAF ReLife
SAF ReLife offers significant benefits that address key challenges in the additive manufacturing (AM) sector. One of the primary advantages is its ability to significantly reduce the carbon footprint of AM processes. According to studies conducted by Fraunhofer IPA, using SAF ReLife can reduce the carbon footprint by up to 89% compared to manufacturing with new PA12 materials. This is a major benefit for industries facing pressure to comply with stringent carbon emission standards.
In addition to its environmental benefits, SAF ReLife offers cost savings. By recycling and repurposing waste powder, it reduces the need for fresh raw materials, leading to lower material costs per part. This is particularly valuable for manufacturers engaged in high-volume production, where material costs can be a significant factor.
The system also enhances production efficiency and waste reduction by diverting powder waste from disposal, helping to lower the amount of waste generated in AM processes. This efficient recycling process extends the life of PA12 powder, reducing the frequency with which new materials are required.
Furthermore, parts produced using SAF ReLife maintain high standards of quality, despite being made from recycled materials. The surface finish and durability of these parts meet the demanding requirements of end-use applications, ensuring that performance is not compromised.
Finally, SAF ReLife aligns with circular economy principles by transforming the traditional linear production model into a circular one. In this model, resources are reused, waste is minimized, and the lifecycle of materials is extended, contributing to more sustainable manufacturing practices.
How SAF ReLife Works
SAF ReLife works by integrating seamlessly with Stratasys’ H350 printer, which employs SAF (Selective Absorption Fusion) technology for the efficient production of parts using a powder bed fusion process. The first step in the process involves collecting waste powder that has been used in previous prints. This waste powder is then carefully filtered, graded, and treated to ensure it meets the specific requirements for additive manufacturing (AM). The recycled powder is blended with fresh PA12 material in carefully controlled ratios to restore its consistency and ensure high performance during the printing process.
Through this method, SAF ReLife ensures that the recycled powder retains its quality, allowing the finished parts to possess the same durability and precision as those made with entirely new materials. This is a critical feature, as it allows manufacturers to reuse materials without compromising the integrity of the parts, making it a highly efficient and sustainable practice. By using this approach, Stratasys not only reduces waste but also decreases the environmental impact of additive manufacturing, offering a significant contribution to sustainability in industrial applications. This method of recycling materials also helps to stabilize material supply chains by reducing dependence on virgin resources, which can be subject to volatility in availability and price.
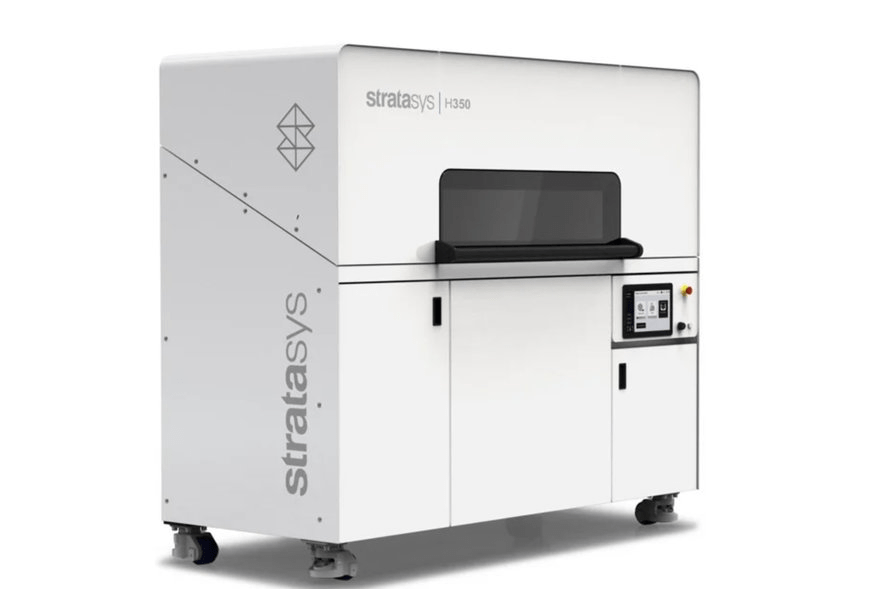
Success Stories: SAF ReLife in Action
Early adopters of SAF ReLife, such as Wehl Green, a service bureau specializing in AM solutions, have already reported notable achievements. During the beta testing phase, Wehl Green observed a 20% reduction in the total cost per part and a significant decrease in waste. Their ability to meet customer demand within 48 hours further underscores the efficiency and speed enhancements afforded by SAF ReLife. By reducing production costs and offering quick turnaround times, SAF ReLife demonstrates a real-world impact in high-demand sectors.
Concrete Solutions Offered by SAF ReLife
SAF ReLife offers a comprehensive solution to a variety of challenges facing the additive manufacturing (AM) industry, especially in the context of increasing environmental concerns and resource management.
As environmental regulations tighten, manufacturers in the AM industry are under growing pressure to minimize their environmental impact. SAF ReLife addresses this need by facilitating compliance with environmental standards, particularly through the reduction of waste. This allows companies to continue operations while meeting regulatory requirements and contributing to more sustainable production practices.
Another significant challenge in AM is the reliance on petroleum-based materials, such as PA12, a key component in powder-based processes. SAF ReLife helps alleviate this issue by recycling waste powder, which reduces the dependence on virgin PA12. This approach conserves natural resources and helps stabilize material supply chains, providing an eco-friendly alternative to traditional sourcing methods.
Traditional AM processes are also notorious for generating large amounts of powder waste that often end up in landfills. SAF ReLife combats this issue by reintegrating excess material into production, drastically reducing landfill contributions and encouraging responsible waste management practices. This not only lowers the environmental footprint but also enhances the efficiency of the manufacturing process.
The ability to reduce raw material costs also provides a significant competitive edge. By lowering production costs, SAF ReLife makes additive manufacturing more accessible, particularly for smaller companies and startups. This democratization of AM technology spurs innovation and encourages a more diverse range of market participants, ultimately driving industry growth.
Finally, SAF ReLife’s scalability makes it a versatile solution across multiple industries, including aerospace, automotive, and consumer goods. By reducing costs and environmental impact, it is especially beneficial to sectors that require precision and high-quality components. This broad applicability ensures that the benefits of SAF ReLife extend beyond any one particular field, helping to shape a more sustainable and efficient future for additive manufacturing.
In summary, SAF ReLife addresses critical industry challenges by promoting waste reduction, material conservation, and cost efficiency, while fostering innovation and ensuring compliance with environmental regulations. This solution has the potential to transform the additive manufacturing landscape, making it more sustainable and competitive across a wide range of industries.
Stratasys: Pioneering Sustainable Additive Manufacturing
Stratasys has long been committed to advancing sustainable practices in AM. SAF ReLife, part of their broader sustainability initiative, addresses the entire lifecycle of AM materials, from production to disposal. This focus on sustainable innovation aligns with the evolving priorities of industries worldwide, where consumers and stakeholders demand more environmentally friendly manufacturing practices.
Stratasys’ commitment to the environment is reflected in their support for research and development in sustainable AM practices. By continuously refining SAF ReLife and related technologies, Stratasys aims to set new standards in the industry, paving the way for a more sustainable future in manufacturing.
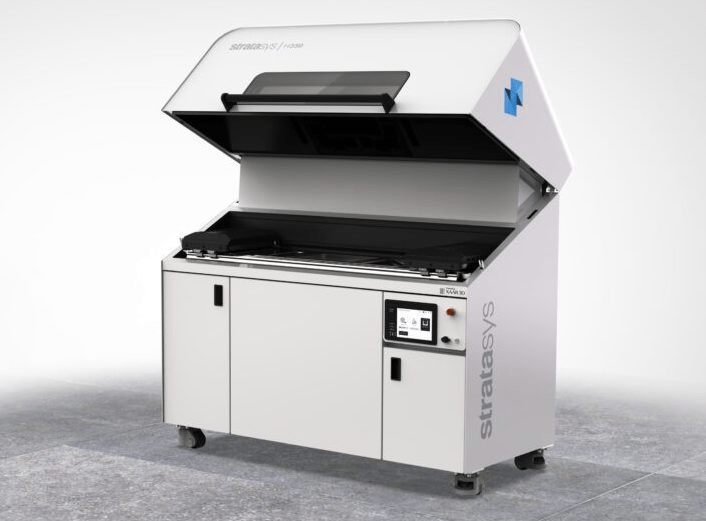
Expanding the Scope of SAF ReLife: Future Potential
The launch of SAF ReLife opens up possibilities for expanded applications in the AM sector. Some potential areas for future growth include:
- Integration with Other Material Types: While SAF ReLife currently focuses on PA12, Stratasys could explore recycling processes for other polymers, including PA11 and TPU, which are also commonly used in AM.
- Automation of Waste Powder Collection and Sorting: Implementing robotic sorting systems to collect and grade waste powder could make SAF ReLife even more efficient and suitable for high-volume production environments.
- Collaborations with Industry Leaders: Stratasys could partner with companies across various sectors to develop custom solutions based on SAF ReLife technology, further promoting sustainable practices in AM.
Beyond SAF ReLife: Comprehensive Sustainable Practices in Additive Manufacturing
While SAF ReLife marks a considerable step forward, achieving sustainability in AM requires a holistic approach. Here are additional sustainable practices that can complement the efforts initiated by SAF ReLife:
- Optimized Material Usage: By carefully controlling the amount of powder deposited during the manufacturing process, companies can reduce excess powder generation, leading to less waste and fewer recycling demands.
- Energy-Efficient Printers: Incorporating energy-efficient mechanisms in printers, such as lower power settings during non-critical operations, can further reduce the carbon footprint associated with AM processes.
- Localized Production Hubs: Establishing local AM facilities to meet regional demands can minimize transportation-related emissions, contributing to a smaller environmental footprint overall.
- Recycling Partnerships: By forming partnerships with recycling companies, AM providers can ensure that any waste generated during production is either repurposed or disposed of in an environmentally responsible manner.
- Biodegradable and Renewable Materials: Research into biodegradable and plant-based polymers can lead to the development of eco-friendly AM materials, reducing the dependency on petroleum-based polymers.
Conclusion: A Path Toward Circular Manufacturing
SAF ReLife represents a significant stride toward circular manufacturing within the AM industry. By turning waste into valuable resources, Stratasys is not only addressing the issue of material waste but also setting an example for sustainable practices in manufacturing. As industries move toward environmentally conscious production methods, SAF ReLife’s waste recycling capabilities showcase how technology can foster a circular economy in AM.
For companies and industries alike, SAF ReLife serves as a reminder that sustainable innovation can bring about both economic and environmental benefits. As we look to the future, the continuous refinement of SAF ReLife and similar technologies will be key to making AM a genuinely sustainable manufacturing solution. Stratasys has opened the door to a new era where additive manufacturing is synonymous with responsibility, resilience, and respect for the environment.
Related Content
- Reducing Sustainability and Waste Impacts Through Carbon Emissions by Country
- Bioenergy: A Sustainable Solution to Energy Waste
- Merit Unveils Eco-Friendly Great Skin Moisturizer Made from Food Waste
- Startup Replaces 6 Million Plastic Bags with Eco-Friendly Corn Waste Alternative
- Heavy-Duty PP Garden Waste Bags Set – Reusable Yard Debris Bags with Industrial Fabric and
- Handles for Plant, Grass, and Leaf Collection – 3 Sizes: 500L, 300L, 120L Pack
- Benepaw Biodegradable Dog Poop Bags Eco-friendly Leak-proof Quality Thick Strong Pet Waste Bags 120/300 Pieces Easy To Tear
- Stratasys Launches SAF ReLife to Repurpose Waste PA12
- Stratasys launches SAF ReLife software solution
- Stratasys Ltd. Announces the Launch of SAF ReLife
- Stratasys H350 Now Powered by New SAF ReLife Solution